Working areas: | Preprojects and technical development Functional- and equipment specifications Mainframe- and PC-computer programming System development for process control- and operation systems Database design and development of information systems Integration between different type of systems |
Products: | INICast, a Metal Measurement System for tiltable aluminium casting furnaces. INICast is patented. |
Some of our customers
- Elkem Aluminium Mosjøen
- Elkem Aluminium Lista
- Hydro Automotive Structures
- Falconbridge
Function description
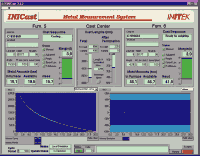
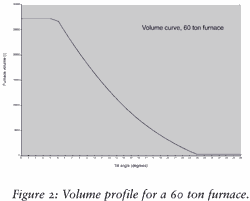
The Norwegian consultant company, INITEK, has developed a computer based system for supervision and con-trol of the molten metal volume in a casting station based on information and measurements that are already available in the casting station or that easily can be established. The system measures the volume of molten metal in the furnace before and during the entire cast as well as the amount of metal in launders, troughs, filters and casting table. The total amount of molten metal is available for the ongoing cast. Furthermore, the remains of metal in the furnace after casting is estimated as well.
The patented method is based on the fact that there is a relation between furnace volume, tilt angle and the metal level in the furnace tap-out. This relation is called the Furnace Volume Profile (FVP). When the FVP is known (calculated by the system) the actual molten metal volume in the furnace is calculated using the tilt angle and the metal level in the furnace tap-out. The volume profile for a furnace will change over time due to phenomena like fouling, wear and tear etc. The system will automatically generate and store a new furnace curve for each cast. These stored curves will be the input for a generation of a new volume profile. The most important reason why the method works in practice, is the fact that there are separate functions in the system for generation and maintenance of the volume profile. Figure 2 shows an example of a volume profile for a 60 ton casting furnace at Elkem Aluminium Mosjøen, Norway which is generated by the system in daily opera-tion.
In determining the metal volume available before casting, the metal volume in troughs, filters and casting table has to be taken into account. A casting station often has various courses for the metal from the furnace to the casting table, depending on metal treatment to be given. This means that the metal volume on its way between furnace and casting table can vary quite a lot from casting to casting. See figure 3. The system takes into account the metal´s course in the station in question to be able to correct these deviations. The system automatically calculates the different volumes at different courses.
Since the system continuously estimates the available metal volume for the cast, the operator can be warned during casting if there is too little metal in the system to achieve the desired casting length. The early warning enables the operator to shut off a few molds early in the casting instead of all the billets becoming too short. At the end of the process, the remains of metal in the furnace is determined. This is the start of the next charge. The remains of metal is an important parameter to achieve the correct metal volume and metal analysis when the next charge is to be alloyed.
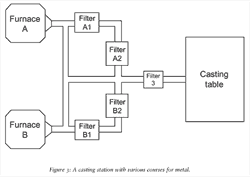
Accuracy considerations
When the metal volume in a casting furnace is to be measured, there will be a need for tarring and calibration functions regardless of measurement system used, due to the fact that the furnace itself change over time, e.g. the lining is being worn. If tarring and calibration cannot be executed at sufficient frequency, the performance of any measurement system will gradually be reduced and the measurement accuracy will be lowered over time.
INICast emphasizes the parts of the system which optimize the measurement accuracy over time, with a minimum of disturbance of operations. In addition, the system has functions which indicate if the measurement inaccuracy increases.
These elements are decisive factors for maintaining accuracy over time. Assuming that the measurements and parameters are accurately fed into the system, the inaccuracy is roughly proportional to the remains of metal in the furnace at any given time, i.e. the accuracy increases at the end of the cast.
The absolute accuracy for a casting station can only be estimated when the station´s parameters are known. Typically, for a 60 ton furnace the accuracy will be approximately +/- 500 – 700 kg at full furnace.
System overview/ System Structure
- The system is contained on a PC located in the control room. It will cover the furnaces that are served from this control room. The system structure is shown in figure 4.
- A high resolution tilt angle sensor must be installed on the furnace.
- At least one good level sensor (SLS5000) must be installed per furnace on the casting station measuring the metal level in the launder (in practice directly after the furnace tap-out).
- The interface between the casting station control system and the INICast System must be defined. Operator displays may be added or changed.
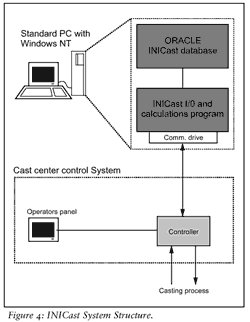